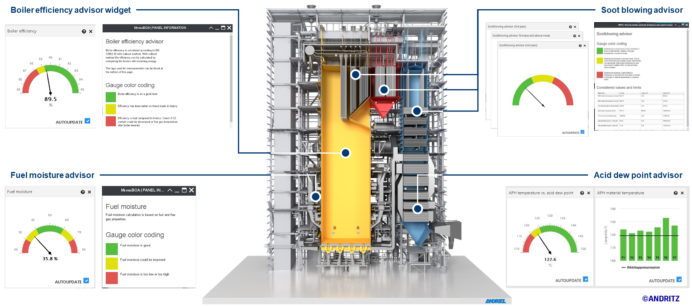
Phasing out the energy use of peat and achieving a considerable increase in the use of recycled fuel. These are two basic reasons that gave rise to development collaboration between Pohjolan Voima and ANDRITZ, a supplier of boiler solutions to power plants, at the Hämeenkyrön Voima biopower plant. The end result is the Metris BOA measurement and analysis system, which extends the service life of boiler equipment, decreases maintenance costs and helps decrease the emissions of the power plant.
Operation manager Tero Siltanen from Hämeenkyrön Voima clicks through menus that allows him quickly to see the sulphur and chlorine balance of the boiler or, for example, the need for soot blowing the boiler. The Hämeenkyrön Voima power plant is a combined heat and power plant. Its biopower plant was completed in 2012. The plant’s boiler was supplied by ANDRITZ.
“These new tools provide us with a real-time picture of the status of the biopower plant. Here we can see that there is a need for soot blowing a part of the boiler, while the situation is fine in the other parts”, Siltanen explains and points at the graphs.
The Metris BOA system demonstrated by Tero Siltanen started as a pilot project, but the tests that started in 2018 and the current operating experience already show that visualised measurement data informs the biopower plant operators of the boiler’s status faster and more precisely than before, and in a format that is easier to handle.
Johannes Bolhar-Nordenkampf, product manager of IIoT solution within ANDRITZ, describes Metris BOA as ANDRITZ web app platform, that is more than just a digital advisor serving the operator with recommendation to keep the boiler process at its optimum. Metris BOA can provide automized reports about performance improvements, Email alerts on KPIs and be the single source of documentation accessible from anywhere via a web browser.
ANDRITZ vision of an autonomous power boiler is the digital operator that interacts with the DCS directly, where machine learning algorithm and artificial intelligence take care of the process and each single equipment.
Siltanen is excited about the new system supplied by ANDRITZ and believes that it will significantly reduce costs and emissions in the long term. Siltanen recently graduated as a Master of Science in Engineering, and also wrote his thesis on the development of reporting at a power plant.
The goal of carbon neutrality guides development
Since 2017, Hämeenkyrön Voima has been increasingly using recycled fuel, i.e. fuel made from separately collected waste from construction, retail and industry. Using replacements for fossil fuels at power plants poses new challenges to power plant technology and energy companies. For example, erosion and corrosion damage to boilers increases, and new methods are needed for the monitoring of sulphur balance and boiler performance. Naturally, Pohjolan Voima’s ambitious carbon neutrality targets also play a part in the background. Solutions that decrease emissions are actively sought all the time. Hämeenkyrön Voima Oy is a subsidiary of Pohjolan Voima.
“When making the switch to recycled fuel, we already knew that the varying quality of the fuel and the impact of the new fuels on the boiler will pose challenges to us. The situation was difficult to control because we could only analyse it during annual maintenance, when we had the chance to look inside the boiler”, says Jarmo Tervo, Manager, Technology and Projects, Pohjolan Voima.
Solutions sought through collaboration
There was a clear need to improve the situation picture obtained from boilers. Because of this, the development of a measurement and analysis system was initiated with ANDRITZ. The goal was to get answers, for example, on how to measure the situation of the boiler in real time, how to continuously monitor fuel quality, which risk of corrosion there is at a given time and how to monitor the boiler’s sulphur balance and dirtiness.
“When discontinuing the use of peat, the feeding of sulphur became an important factor. There was a need to know how much sulphur is needed: too little and too much both lead to problems. The new system automatically uses the right amount of sulphur, decreasing corrosion in the boiler”, Tervo says.
“Answers to seemingly innocent process related questions – e.g what is the corrosion risk in superheater area now, or when did the fuels that we’re firing now arrived to the site – demand potentially a lot of complicated calculations or a chain of reasoning that might come naturally only to a process specialist. Because all necessary data refining is not feasible or even possible to do in the automation system, it has been our goal in the Metris BOA project to bring the substance knowledge of process specialists into digital services, in which we can choose the most suitable tool for each use case”, Antti Rossi, BOA development manager at ANDRITZ says.
One measurement functionality included into the analysis system was intended for the optimisation of the fuel mix and the maximisation of operating efficiency.
“Fuel is the greatest cost factor. Keeping the fuel mix optimal is one way to achieve the best cost savings and emission reductions”, Tervo adds.
Benefits already obtained from the pilot project
According to Jarmo Tervo, the technology expert ANDRITZ was the perfect partner for Pohjolan Voima, because the company has expertise in boilers and is interested in developing analytics related to them.
“Data alone is not enough: we also need the means to analyse the data and an understanding of what to do based on the data. It was clear to us that in any case, our knowledge of risks, their management and operating the plant will grow with this pilot project”, Tervo says.
The development work carried out at the plant is already providing benefits. They come from decreased emissions, the control of maintenance costs and the management of availability. In addition, the quality of ash has improved at the plant.
“This pilot project is a part of Pohjolan Voima’s determined development work towards ending the use of fossil fuels and achieving the company’s carbon neutrality targets. For example, the work to end the use of peat has been ongoing for a really long time”, Tervo points out.
“In this project with Hämeenkyrön Voima we have been able to get close to the everyday life of our customer and think together the ways in which refining the plant data from different sources can add value. It has been also very valuable to have our end customers, the operators, along in the development of the product”, Rossi adds.
Tero Siltanen, the operation manager of the plant, also praises the development work with ANDRITZ.
“The collaboration has been smooth and very successful. We’ve been able to advance matters together. It has also been a great opportunity for myself to get to participate in this kind of a digitalisation project”, he says.
ANDRITZ is a globally leading supplier of plants, equipment, and services for hydropower stations, the pulp and paper industry, the metalworking and steel industries, and for solid/liquid separation in the municipal and industrial sectors as well as for animal feed and biomass pelleting. Other important business segments include automation and service business.
Plants for power generation, flue gas cleaning, recycling, and the production of nonwovens and panelboard complete the global product and service offering. Innovative products and services in the industrial digitalization sector are offered under the brand name Metris and help customers to make their plants more user-friendly, efficient and profitable. The publicly listed technology Group is headquartered in Graz, Austria and has a staff of approximately 26,700 employees located all over the world and operates more than 280 sites in over 40 countries.
ANDRITZ offers Bubbling Fluidized Bed (PowerFluid) and Circulating Fluidized Bed (EcoFluid) technologies for boilers producing steam and electricity from renewable fuels. These technologies employ proven, yet modern techniques to efficiently produce power while keeping the emissions within environmentally safe limits. The different technologies are distinguished by capacity, fuel, and applications.
The first step towards autonomous power boilers is our digital advisor Metris BOA – a web application that utilizes big data (B) to optimize (O) and analyze (A) the power plant processes and monitor the equipment installed. The Center of Excellence for Metris BOA is located in Finland.
For more information about Metris BOA go to ANDRITZ product homepage www.andritz.com/metris-boa or contact ANDRITZ directly via email metris.boa@andritz.com
or by phone, Johannes Bolhar-Nordenkampf, Product Manager IIoT, ANDRITZ AG,
tel. +43 (676) 89501 4785
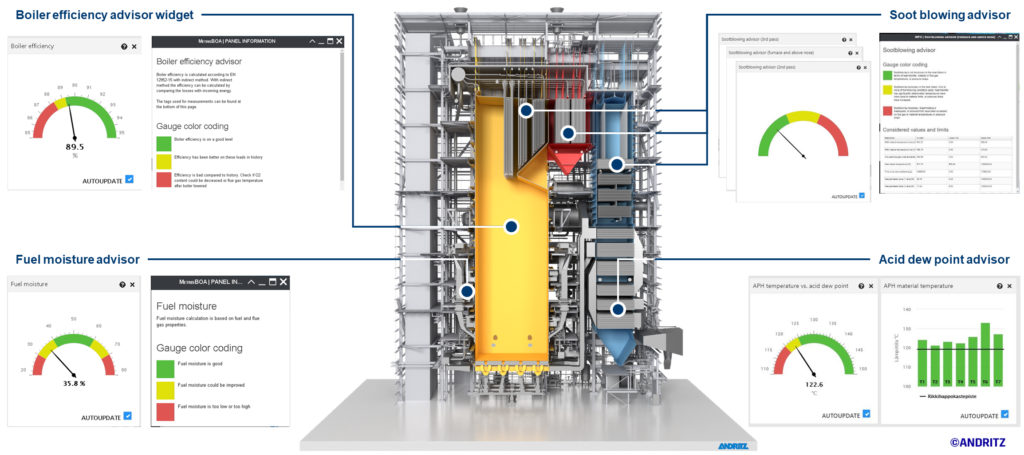
Picture: Metris BOA, ©ANDRITZ